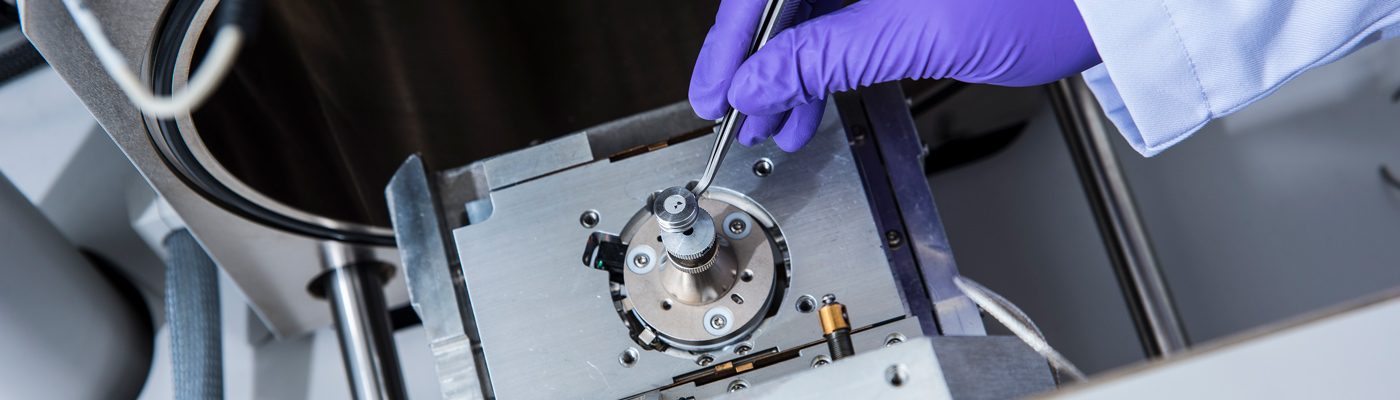
Impact
Our research partnerships within industry ensure maximum impact of research and development.
Explore our case studies below.
Accident-tolerant fuel
Our researchers are focusing on developing solutions to help nuclear reactors to deal with accidents better.
Elemental analysis for nuclear decommissioning
We're working with Sellafield Ltd to improve the way the nuclear industry can clean up and recycle waste.
Radiation effects in waste packages
Monitoring the effects of radiation in disposed-of nuclear waste over a number of years.
Radioactive effluent treatment
We're working with Sellafield Ltd to improve the way the nuclear industry can clean up and recycle waste.