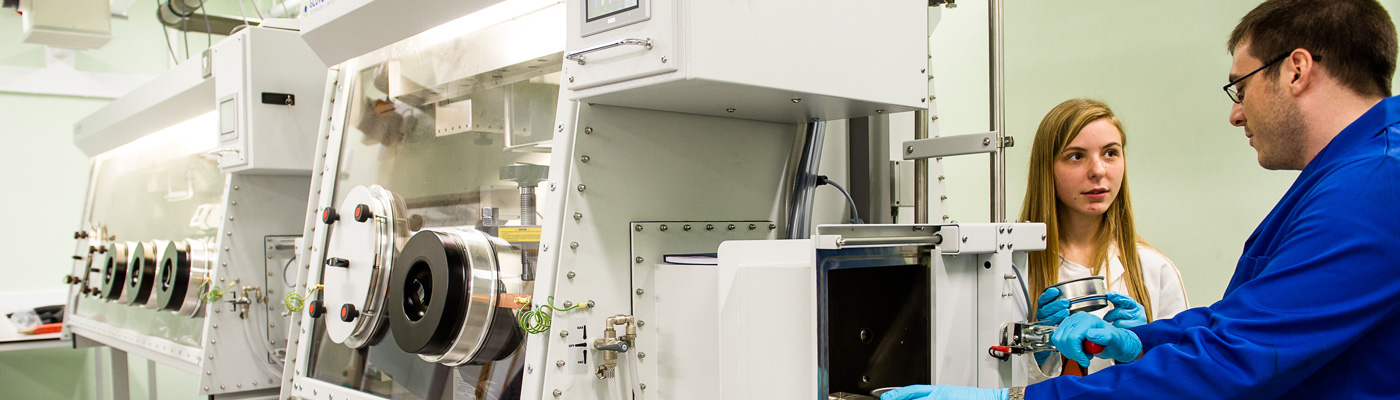
Accident-tolerant fuel
Our researchers are developing nuclear fuel solutions with increased tolerance to high temperatures.
The background
Centre of Excellence
The University is the academic host for the UK's Nuclear Fuel Centre of Excellence, providing extensive capabilities for the manufacture, characterisation, and testing of uranium and thorium fuels.
In water-cooled nuclear reactors, the most critical component in fuel assemblies is the cladding, which encapsulates the fuel, retains any fission products produced during the nuclear reaction and transfers heat generated by the fuel to the surrounding water.
Currently, a zirconium alloy cladding is used but this is prone to failure during accident conditions, as highlighted by the Fukushima Daiichi incident in 2011.
The challenge
After the earthquake near Fukushima Daiichi nuclear power station, the reactors shut down immediately but fission products in the fuel continued to release decay heat.
Zirconium alloys oxidise rapidly at temperatures a few hundred degrees higher than normal operating temperatures, potentially leading to disintegration of the fuel rods.
Rapid corrosion of the cladding also releases hydrogen, and in an accident scenario, this can result in explosions.
The solution
Our researchers are developing accident-tolerant fuel solutions which would provide more grace time (the time before active cooling is required) or, ideally, be immune to the kind of sustained high temperatures created by decay heat and insufficient cooling.
The University of Manchester is the academic host for the UK’s Nuclear Fuel Centre of Excellence, providing extensive capabilities for the manufacture, characterisation, and testing of uranium and thorium fuels.
Fuels can be subjected to ion beam and gamma irradiation at our Dalton Cumbrian Facility. Potential solutions include composite silicon carbide cladding, and advanced fuel materials, such as uranium silicide.
The benefits
By engineering nuclear fuel and cladding materials that can withstand a loss of coolant accident for longer or even indefinitely as compared to current materials, severe consequences of an accident scenario can be significantly reduced and even negated.
The benefits also increase the passive safety of the reactor and so may drastically reduce potential costs of new nuclear build by removing backup safety systems.